Agricultural
Pine Island Farm, Sheffield, MA
A family-owned and operated dairy farm in Berkshire County, Pine Island Farm spans 1,300 acres of cropland, houses approximately 1,000 head of Holstein cattle, and produces and sells 12 million pounds of milk from 750 cows annually. A fully-grown milking cow can produce upwards of 100 pounds of manure per day, which can create odors and - due to carbon dioxide and methane produced during decomposition - greenhouse gas emissions. Prior to 2011, manure at the farm was stored in a 4.1-million-gallon slurry tank and spread on cropland as fertilizer. That changed in November 2011, when Pine Island Farm began using the manure as feedstock for its new anaerobic digester with a combined heat and power (CHP) energy system. Today, the digester takes in mostly manure; up to 8-10 percent of the feedstock is excess whey from a regional dairy processor. With electrical generation capacity of 225 kilowatts, the farm's organics-to-energy conversion system generated more than 1.1 million kilowatt hours (kWh) of renewable electricity in its first eight months of operation. The energy produced covers all of the farm's electricity use, helps heat its water, and runs the digester equipment, while still enabling the farm to sell power back to the grid. For Pine Island Farm, anaerobic digestion technology has multiple benefits: it enables a more sustainable practice for manure management that also generates renewable power, cuts greenhouse gas emissions, reduces the need for petroleum-based fertilizers, helps protect groundwater from manure leakage, and is estimated to reduce odors by about 75 percent. Moreover, Pine Island Farm can now contribute energy to the New England electric grid, helping to diversify Massachusetts' energy supply through domestic renewable resources.
Jordan Dairy Farms, Rutland, MA
In business since 1941, Jordan Dairy Farms is a fifth-generation, family-owned and -operated farm with 300 milking cows. In 2010, Jordan Dairy joined four other Massachusetts farms to form AGreen Energy , LLC, a partnership designed to enable the farms' transition to more sustainable manure management practices. All five farms plan to adopt anaerobic digestion technology with combined heat and power (CHP) conversion units to transform manure into renewable energy. Jordan Dairy, the first of the five farms to build an anaerobic digester, also partnered with Casella Resource Solutions to bring in source-separated organics from several local food companies (including HP Hood & Sons, Cabot Creamery, Kayem Foods, and Cains Foods) to convert their food waste to energy instead of sending it to landfills. The Jordan facility takes in 9,125 wet tons of manure and 16,425 tons of source-separated organics per year. The system has a capacity of 300 kilowatts and is estimated to generate 2.24 million kWh of electricity per year, enough to power the farm and 300 homes. Thus, with the added organics, one cow at Jordan Dairy Farms produces slightly more electricity than is needed to power one average home. The digestion system works so well that Jordan Dairy is considering increasing the engine size.
As a sustainable waste management option, anaerobic digestion improves air and water quality, mitigates odors, and reduces farm greenhouse gas emissions. In addition, Jordan Farms uses the solids from the digestate for animal bedding and the liquid as a valuable fertilizer, lowering costs further and increasing overall crop yields. The anaerobic digestion projects at the five AGreen Energy farms will diversify their operations, providing farm owners with additional revenue and helping to keep small-to medium-sized farms in business. When fully operational, the anaerobic digesters at all five farms could collectively handle up to 15 percent of Massachusetts' source-separated organics, using it to generate local, renewable energy.
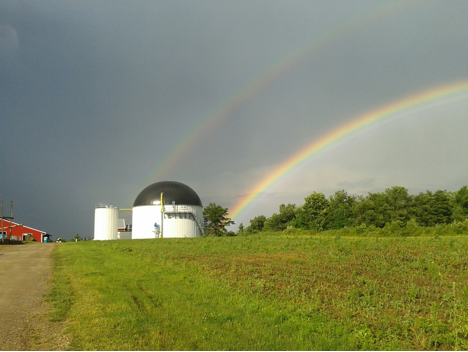
The Jordan Dairy Farm digester and CHP system (Rutland, MA) combines the farm's own dairy cow manure with byproducts from regional food processing companies to make heat and electricity. (Photo Credit: Randy Jordan)
Industrial
Gills Onions, Oxnard, CA
Gills Onions, one of the nation's largest producers of fresh onions, peels up to one million pounds of onions per day, generating roughly 300,000 pounds of onion skins and trimmings. Prior to 2009, Gills Onions used a labor-intensive disposal method to spread the waste over nearby fields and leave it to decompose. This process led to the release of greenhouse gases and odors, attracted pests, and created the potential for groundwater contamination. Gills Onions investigated available waste-management practices and settled on anaerobic digestion as a potential solution, partnering with the University of California-Davis to tailor the available technology to onion trimmings. The result was the Advanced Energy Recovery System (AERS), which has been in operation at Gills Onions' Oxnard facility since July 2009 and handles 100 percent of the facility's onion waste. Within AERS, juice is pressed from onion peels and fed into an anaerobic digester to produce methane-rich biogas, while the remaining material is pressed into nutritive cattle feed. The biogas can be used in place of natural gas with some processing, and it has replaced 112,000 standard cubic feet of piped-in natural gas per day at the facility since 2009. The system provides 600 kilowatts of power - enough to fulfill 100 percent of the Oxnard facility's electricity base load (and equivalent to the electricity needed to power approximately 460 homes). The waste-to-energy system is a win-win for Gills Onions: it provides dependable, on-site power generation - crucial for a large facility that relies on constant refrigeration of fresh onions - and saves $700,000 annually in electrical costs and $400,000 in hauling disposal costs.
At Gills Onions, anaerobic digestion technology has transformed a waste management problem into profits. For its innovative approach to onion waste management, Gills Onions was awarded the 2009 Governor's Environmental and Economic Leadership Award (GEELA) and the 2010 Grand Conceptor Award by the American Council of Engineering Companies (ACEC). Gills Onions has been featured on Huell Howser's California Green and on the Discovery Channel.
PurposeEnergy, Inc. and Magic Hat Brewing Company, Burlington, VT
Brewing beer is messy: along with beer, the process yields spent grain, yeast, and wastewater. Breweries must pay - typically, by the pound - to transport their organic waste off-site to treatment facilities, or sell or give it away to farmers for animal feed. Anaerobic digestion technology provides another option - allowing breweries to convert their organics into energy that can be used on-site. To help breweries use their waste more sustainably, Eric Fitch, CEO of Arlington, MA-based PurposeEnergy, Inc., developed a new anaerobic digestion process tailored to high-solids organics from breweries. After a successful 2006 pilot project at Yuengling's brewery in Tampa, Florida, PurposeEnergy partnered with the Magic Hat Brewing Co., located in Burlington Vermont, to install an industrial-scale facility. PurposeEnergy pays Magic Hat $1/year to lease land adjacent to the brewery for its anaerobic digester. The company takes in Magic Hat's brewery waste and uses it to generate methane-rich biogas, which is converted into renewable electricity that is used within the brewery. The 492,000-gallon digester transforms brewery organics into 50 cubic feet of biogas per minute, generating 300 kilowatts of power, as well as heat to maintain the temperature of the bioreactors. Excess electricity is sold back to the grid. Magic Hat produces about 180,000 barrels of beer annually, and PurposeEnergy helps the brewery save $1.67 per barrel. The anaerobic digestion technology reduces the brewery's dependence on fossil fuels, takes the strain off of local wastewater systems, and productively recycles the brewery's organics to generate on-site power.
For its innovative approach to brewery organics management, PurposeEnergy has received numerous accolades. In 2010, it was selected by AlwaysOn as a GoingGreen Top 50 Winner on the criteria of innovation, market potential, commercialization, stakeholder value, and media buzz. In 2011, the company made Enterpreneur.com's annual list of 100 Brilliant Companies. Additionally, the PurposeEnergy facility at the Magic Hat Brewery was given an Honorable Mention for Renewable Project of the Year in 2010
Youtube Video: Magic Hat Turns Beer into Energy - Purpose Energy, Inc.
Additional Resources
Wastewater
Deer Island Wastewater Treatment Plant, Massachusetts Water Resources Authority, Boston, MA
The Massachusetts Water Resources Authority (MWRA) provides wastewater treatment for 43 communities in the greater Boston area, treating 365 million gallons of sewage per day at its Deer Island Wastewater Treatment Plant, the second largest in the United States. Following primary and secondary wastewater treatment, Deer Island's 12 egg-shaped anaerobic digesters reduce the volume of sludge solids by about 60 percent and produce biogas. The biogas fuels steam boilers that supply heat and hot water for the plant's processes and facilities. The steam also powers a turbine generator that produces about 28 MWh of electricity per year. This co-generation facility supplies more than 97 percent of the treatment plant's thermal and 17.5 percent of its electrical demands, and saves MWRA approximately $15 million in fuel oil costs and $2.5 million in electricity costs annually. The digested sludge flows by pipeline to another facility where most of the water is removed (and sent back to Deer Island for treatment) and the solids are dried into pathogen-free, pelletized fertilizer. Overall, the anaerobic digestion process is key to making a valuable product and allows the treatment plant to use local renewable resources in place of fossil fuels for a significant portion of its energy needs. Starting in mid-2014, MWRA plans to pilot the co-digestion of "source-separated organic matter" (mostly food waste) with the sewage sludge in one or two of its digesters. The additional organic matter will boost the production of biogas and enable the Deer Island plant to produce more of its own energy and save even further on energy purchases.
Greater Lawrence Sanitary District, North Andover, MA
Located on the Merrimack River, the Greater Lawrence Sanitary District (GLSD) operates a wastewater treatment facility that serves the communities of Lawrence, Methuen, Andover, and North Andover in northeastern Massachusetts, as well as the southern New Hampshire town of Salem. In 2002, GLSD built three anaerobic digesters to process wastewater sludge. Today, the three digesters process an average of 135,200 gallons of wastewater sludge and 48,000 pounds of septage per day. The resulting biogas is used in place of natural gas to heat the plant and to dry the biosolids (treated sludge) into pathogen-free pelletized fertilizer in a facility operated by the New England Fertilizer Company (NEFCO). Processing waste through anaerobic digestion reduces GLSD's energy needs and greenhouse gas emissions, all while sustainably managing wastewater sludge.
In 2014, GLSD began a construction project to add a fourth digester tank and two combined heat and power engines with the goal of co-digesting food waste organics with the sludge and using the additional biogas to generate up to 3.2 MW of electricity in addition to drying sludge pellets. The addition of the two CHP engines will also allow the facility to operate in island mode in the event of loss of power from the grid. In January 2017, GLSD started up its food waste organics pilot program to start accepting organics into existing digesters as construction continued. By February 2018, the facility was managing 19,000 gallons per day and ramped up to 26,000 gallons per day by summer 2018. GLSD anticipates the new digester tank and engines will be operational by late fall, 2018, with an ultimate goal of managing 140,000 gallons of food waste organics with the sludge.
Additional Resources
Stand-Alone
Fremont, Michigan Community Anaerobic Digester
The Fremont Community Digester plant, located in Fremont, Michigan, processes more than 100,000 tons of food waste annually to produce biogas, electricity, and soil amendment. This system was developed by NOVI Energy and uses a complete mix anaerobic wet digester that can efficiently process a variety of feedstock. Three one-million-gallon digester tanks accept waste from a wide variety of sources, including food industry processing waste, dairy products, ethanol production byproducts, and industrial glycerin and alcohols, and process these materials over an approximate 22-day period in an oxygen-free environment. Local companies such as Gerber and McDonald's contribute waste to the digester, providing them with an effective way to manage their production waste. The developer has been able to secure 20- or 30-year contracts with some source-separated organics providers, ensuring sustainability of the facility over the long-term. This wet digester system can switch between thermophilic (115-160 degrees Fahrenheit) and mesophilic (86-104 degrees Fahrenheit) processes as necessary, but regularly runs at thermophilic temperatures. Thermophilic systems offer faster reaction rates and shorter processing times, but are generally more sensitive to changes in system temperatures, which can affect methane production. Biogas from the digester runs generators totaling 3 megawatts (MW) in capacity, and all electricity produced is sold to a local utility under a 20-year contract.
The Michigan state law requiring utility companies to obtain 10 percent of their power from in-state renewable sources by 2015 has helped to enable this $22 million project, which was also secured by a $12.8 million U.S. Department of Agriculture Rural Development Loan Guarantee. In the future, the operator plans to use excess heat from the facility's generators to heat and circulate hot water through the industrial park for use by other companies.
University of Wisconsin-Oshkosh
In 2006, the University of Wisconsin (UW)-Oshkosh was one of four UW campuses selected by Wisconsin's then-Governor Jim Doyle to take part in an energy independence pilot program. In short, UW-Oshkosh was challenged to produce or acquire enough renewable energy to offset all of its energy consumption. The campus adopted a comprehensive sustainability plan in 2008 and, armed with an aggressive Climate Action Plan, aims to achieve full carbon neutrality (i.e. offset all campus carbon emissions through energy efficiency and renewable power generation) by 2025. As part of its efforts, UW-Oshkosh completed construction in 2011 on an anaerobic digester and a combined-heat-and-power (CHP) conversion unit located directly across a river from the main campus. The facility was constructed by BioFerm Energy Systems through a public-private partnership, and is owned and managed by the UW-Oshkosh Foundation. The project has an expected lifetime of 20 years and a simple payback time of 10 years. Any profits to the UW-Oshkosh Foundation will fund student scholarships.
While most anaerobic digesters process "wet" materials, the UW-Oshkosh facility is the nation's first commercial-scale "dry" biodigester, meaning that the plant takes in source-separated organics in solid form instead of liquid slurries. At UW-Oshkosh's Reeve Memorial Union, students are encouraged to "Feed the Beast" by putting their food waste, napkins, and pizza boxes into separate receptacles for the anaerobic digester. The digester takes in 8,000 tons of food and yard waste annually; some of this feedstock comes from the campus, but the bulk is supermarket produce and yard waste collected by the City of Oshkosh. The source-separated organics are processed to yield biogas and biosolids that are similar to late-stage compost. The solid materials are sold within the state as fertilizer, and the biogas is used to maintain constant temperatures throughout the digester process and to produce electricity, which is sold back to the grid. As of summer 2012, the facility was operating at 50 percent capacity. When fully operational, it will be able to provide up to 10 percent of the campus's electricity and heat. UW-Oshkosh is also using the digester as a learning tool: the school invites visitors to come and see the system in action, and students collect data on the digester feedstock to determine its optimum composition. At UW-Oshkosh, anaerobic digestion is moving the campus closer to achieving its ambitious sustainability goals by generating clean, local, renewable energy.
Green Bin Program and Dufferin Organics Processing Facility, Toronto, ON
Through its Green Bin Program, the City of Toronto incorporates an environmentally-conscious option for source-separated organics processing directly into its Municipal Waste Management system. Residents of Toronto separate their organics and recyclables from the remainder of their waste, and the city collects the organics in special green bins. The residential organics are transported to the Dufferin Organics Processing Facility, which is located just outside of the city and has been operational since 2002. Inside, the facility maintains negative air pressure to prevent odor release, and the waste is sorted further to remove any unwanted materials. An anaerobic digester processes the sorted organics - approximately 770 tons per week - to generate biogas and solid digestate. The digester solids provide feedstock for a privately owned composting facility. The biogas is flared to reduce greenhouse gas emissions, preventing the average weekly release of 29,588 cubic meters of methane. The city is considering facility upgrades that would capture the biogas and use it as fuel.
The Green Bin Program has a participation rate of 98 percent among city residents, and it has been able to capture and divert more than 91 percent of the city's organics from the landfill. Through citizen participation and public initiative, Toronto has successfully implemented and maintained a sustainable option for the disposal of organic waste, reducing the amount of waste it sends to landfills and its environmental footprint. Due to the Dufferin plant's success, Toronto is currently planning to build two more anaerobic digestion facilities to sustainably process even more of its waste.
University of California-Davis & CleanWorld Partners, Davis and Sacramento, CA
Since 1998, University of California-Davis Professor of Biological and Agricultural Engineering Ruihong Zhang has been working on anaerobic phased solids (APS) and high-rate digestion (HRD) technologies to more effectively process high-solid organic wastes and use water more efficiently. Professor Zhang's work is an ideal complement to sustainability efforts currently underway in the Bay Area, such as the City of Davis' 2008 Climate Action and Adaptation Plan, which calls for a 15 percent reduction in greenhouse gas emissions by 2015 and full carbon neutrality by 2050. In addition, several local food waste producers, including Wal-Mart and Campbell's Soup, have committed to sustainability and need the proper infrastructure to help them follow through. In 2006, Professor Zhang and UC-Davis partnered with Onsite Power Systems and CleanWorld to build a pilot facility at Davis using the new digestion technologies. On Earth Day 2014, the university and CleanWorld officially unveiled the UC Davis Renewable Energy Anaerobic Digester (READ) at the campus' former landfill. The system is designed to convert 50 tons of organic waste to 12,000 kWh of renewable electricity each day using state-of-the-art generators, diverting 20,000 tons of waste from local landfills each year.
The facility took unique advantage of its location at the now closed UC Davis landfill by blending landfill gases — primarily methane — with the biogas to create a total of 5.6 million kWh per year of clean electricity. It is expected to reduce greenhouse gas emissions by 13,500 tons per year.
The READ BioDigester encompasses several of the university's goals: reducing campus waste in a way that makes both economic and environmental sense, generating renewable energy, and transferring technology developed at UC Davis to the commercial marketplace. Nearly half of the organic waste, or feedstock, needed to operate the biodigester will come from UC Davis dining halls, animal facilities and grounds. CleanWorld is working with area food processing and distribution centers to supply the remaining amount. Meanwhile, UC Davis will earn 100 percent of the project's green energy and carbon credits and receive all of the electricity generated. Whatever is not turned into biogas can be used as fertilizer and soil amendments — 4 million gallons of it per year, which could provide natural fertilizers for an estimated 145 acres of farmlands each day.
The first commercially-available anaerobic digester using Professor Zhang's technology, developed by CleanWorld, began operating at American River Packaging (ARP) in Sacramento in April 2012. Each day, the digester takes in 7.5 tons of food waste and a half-ton of corrugated packing material from ARP to generate roughly 1,300 kilowatt-hours of renewable energy. This process meets 37 percent of ARP's electricity needs and prevents 2,900 tons of organics from ending up in landfills annually.
CleanWorld also built a digester and a renewable natural gas fueling station in south Sacramento. The Organic Waste Recycling Center is now processing 25 tons of food waste per day and construction is underway to expand the facility to 100 tons per day, converting the organics into 700,000 gallons of compressed natural gas to be used as fuel for both public and private vehicle fleets.
More Information:
Columbus Anaerobic Digester, Columbus, OH
Since December 2010, an anaerobic digestion facility just outside Columbus, Ohio, has been processing sewage sludge and food remains to create renewable energy. Located less than a mile from the nearest residential area, the facility collects biogas from the controlled decomposition of organic wastes and uses it to generate daily up to one megawatt of renewable power and compressed natural gas (CNG) equivalent to the energy supplied by 3,600 gallons of gasoline. The Columbus facility also houses a CNG fueling facility, giving vehicle owners an option for renewable fuel. The digester is owned and operated in a public-private partnership between the Solid Waste Authority of Central Ohio (SWACO), Kurtz Bros. Inc., an experienced Ohio-based landscape and resource management business, and Quasar Energy Group (http://www.quasarenergygroup.com/), another Ohio-based company with a mission of generating affordable, renewable energy from organic matter. Quasar also operates other AD systems in Ohio, and partners with researchers at The Ohio State University's Agricultural Research and Development Center (OARDC) to improve the performance of AD processes. The Columbus AD facility, just one product of these organizations' combined expertise, is helping Ohio meet its aggressive renewable energy goals while changing the way Ohio and its institutions think about waste management. In a sustainable hole-in-one, the Memorial Tournament, an annual PGA tour golf tournament, worked with SWACO and Kurtz Bros. in 2012 to dispose of the event's 5-10 tons of food remains in the Columbus digester. This effort, just one proactive step the Memorial Tournament is taking towards sustainability, brought the event closer to being "the greenest stop on the PGA Tour."
Related Videos
Youtube Video: Powering A New Generation (2014)
Youtube Video: Biodigester Feed the Beast
Youtube Video: Biodigester Turns Waste into Campus Energy at UC Davis
Youtube Video: Biogas - Anaerobic Digester Build (Time-Lapse)