Download this Fact Sheet as a PDF
Disclaimer
Note that the following text summarizes only those EPA regulations that pertain to air emissions from spray painting operations. The EPA has numerous other regulations that auto shops must comply with, most notably regulations governing management of hazardous waste and used oil (see the “Hazardous Waste Management” fact sheet) and regulations on industrial wastewater (see the “Wastewater Management” fact sheet).
For compliance assistance questions, contact: Anne McWilliams at 617-918-1697 or Susan Lancey at 617-918-1656.
Also note that the following text only summarizes those MassDEP regulations that pertain to spray painting operations. Shop owners should refer to the original regulation – 310 CMR 7.18(28) – for the full range of requirements.
EPA’s “NESHAP 6H” Regulation
All auto body shops that spray coatings (e.g., primers, paints, clear coats) onto motor vehicles must comply with the EPA regulation entitled “Paint Stripping and Miscellaneous Surface Coating Operations: National Emission Standards for Hazardous Air Pollutants (NESHAP) for Area Sources.”
This regulation, at 40 Code of Federal Regulations Part 63, Subpart HHHHHH, is often referred to as the “6H” rule. See EPA’s Paint Stripping and Miscellaneous Surface Coating Operations rule summary for more information. lt applies to area sources that carry out any of these activities:
- Paint stripping operations that use methylene-chloride (MeCl)-containing paint stripping formulations;
- Spray application of coatings to motor vehicles and mobile equipment;
- Spray application of coatings to a plastic and/or metal substrate where the coatings contain compounds of chromium (Cr), lead (Pb), manganese (Mn), nickel (Ni), or cadmium (Cd).
An “area source” emits or has the potential to emit less than 10 tons per year of individual hazardous air pollutants (HAP) or 25 tons per year of combined HAP.
Your shop must meet both the 6H requirements and the related requirements of MA DEP, which are in some cases more stringent.
6H: What You Need To Know
Painter Training Documentation
All painters must be trained in spray gun equipment selection, spray techniques, maintenance, and environmental compliance. Painters must receive refresher training or recertification every 5 years. Shop owners must maintain documentation certifying that painters have received this regulation’s required training. Ask your paint manufacturer or vendor if they offer free NESHAP 6H trainings for customers. EPA has found that these training requirements are efficient pollution prevention, in that the capital cost to comply with the regulations are offset and recovered over time as a result of more efficient use of labor and materials.
Spray Booth Filter Efficiency Documentation
Under 6H, spray booths must be equipped with exhaust filters that achieve at least 98 percent collection efficiency for paint overspray. (Note: Spray applications involving less than 3 fluid ounces of material are not required to take place in a spray booth. However, it is a good practice to apply all coatings in your spray booth to eliminate any compliance questions from regulators or neighbors.) Shop owners must maintain documentation (e.g., manufacturer specifications) demonstrating that at least 98 percent filter collection efficiency is met. Spray booths used to refinish complete motor vehicles or mobile equipment must be fully enclosed and ventilated at negative pressure (or up to 0.05 inches water gauge positive pressure, for booths that have seals on all doors and other openings and an automatic pressure balancing system). Spray booths or stations used to coat miscellaneous parts or products or vehicle subassemblies must have a full roof, at least three complete walls or side curtains, and be ventilated so that air is drawn into the booth.
Spray Guns
All coatings must be applied with high volume low pressure (HVLP) spray guns, electrostatic application, airless or air-assisted airless spray guns, or an equivalent technology. Paint spray gun cleaning must be done so that an atomized mist or spray of the cleaning solvent is not created outside of a container that collects used gun cleaning solvent.
Massachusetts regulations (see below) require use of enclosed spray gun cleaning machine. See the “Water-Based Gun Washing” fact sheet for information on safer and effective alternative gun wash chemicals and view this case study on how 912 Auto Center saved thousands of dollars per year by switching to an EPA-approved gun wash.
Reporting
EPA requires three types of reports to be filed:
- Initial notification – informs EPA that the facility is subject to the standards and when the source will be in compliance.
- Notification of compliance status – certifies that the source is in compliance with the applicable requirements. New sources must certify within the initial notification.
- Annual notification of changes report – required each calendar year any reportable changes occur.
If your shop has not yet submitted any of these 3 reports to EPA, consult OTA for free and confidential assistance, or directly with the EPA about how best to comply with this requirement. New shops should notify the EPA as soon as possible. Submit your reports to: EPA Region I, United States Environmental Protection Agency – New England, 5 Post Office Square, Suite 100 (Mail Code: OES04-2), Boston MA 02109-3912, Attn: Air Clerk.
Exemptions
If you can prove that none of your coatings contain cadmium, chromium, lead, manganese, or nickel, you can petition the EPA for an exemption from 6H. Many popular paint manufacturers (such as Sherwin Williams, Sikkens, PPG- also see PPG’s ‘Area Source Rule Exemption Qualifying Products List’ at the bottom of the page - etc.) will provide you with lists of NESHAP regulated coatings or coatings that do not contain target compounds, Ask your supplier or paint manufacturer for a list of products containing these target compounds in your coating lines, and refer to the fact sheet on “Less Toxic Alternatives” for further information on this topic.
Paint Stripping Operations
Auto shops that use methylene chloride (MeCl) must maintain records of annual usage of MeCl containing paint strippers. Paint stripping operations using methylene chloride (MeCl) must implement management practices that minimize emissions of MeCl, including:
- Evaluating the need for paint stripping (i.e., is it possible to re-coat without stripping?).
- Evaluating each application to identify potential alternative stripping methods.
- Reducing exposure of strippers to air.
- Optimizing application conditions.
- Practicing proper storage and disposal.
Even if you are exempt from NESHAP 6H, you still need to comply with the MassDEP regulations found below as well as local regulations.
Find Additional Information
This EPA fact sheet summarizes the “NESHAP 6H” requirements. The full regulation is also available online.
MassDEP Auto Refinishing Regulations
Massachusetts auto body shops are regulated by 310 CMR 7.18(28), and apply to anyone “who owns, leases, operates, or controls an automotive refinishing facility.” Regardless of whether you are exempt from the EPA’s NESHAP 6H requirements; you must also follow state regulations.
MassDEP: What You Need To Know
VOC Limits
Massachusetts regulations set limits to the amount of volatile organic compounds (VOCs) that can be found in surface preparation products or coating materials. Massachusetts vendors are required to sell only VOC-compliant coatings. All components of the coat (paint, hardener, and reducer) must be mixed so that the total VOC content is less than the set limits identified below.
Storage and Disposal
Use tightly-closed containers to store fresh and spent solvent, coatings, sludge, and rags used during surface preparation or other solvent cleaning operations. All wastes must be disposed of or recycled properly. See the “Hazardous Waste Management” fact sheet for more information.
Spray Equipment
Coatings must be applied using one of the following methods:
- HVLP spray equipment that is operated and maintained in accordance with the manufacturer's recommendations.
- Electrostatic application equipment that is operated and maintained in accordance with the manufacturer's recommendations.
- Another approved coating application method. Approval should be obtained from MassDEP in writing.
Spray Gun Cleaning Requirements
Spray guns must be cleaned in a device that minimizes solvent evaporation during cleaning, rinsing, and draining operations, re-circulates solvent during the cleaning operation so that the solvent is reused, and collects spent solvent so that it is available for proper disposal or recycling. This is what is commonly known as a spray gun washer. For more information, see the “Alternative Gun Washing” fact sheet.
Training Requirements
All paint technicians must receive training and instruction in the proper operation and maintenance of the spray equipment and spray equipment cleaning device(s).Talk to your supplier or paint manufacturer to see if they offer training.
Recordkeeping Requirements
You must maintain monthly purchase records of coatings and surface preparation products on site for three years. Some paint suppliers keep track of this on your online account, or can help you keep track of your records – ask them for this service. Records must include:
- Each coating category, coating or coating component, and surface preparation product as identified on the container.
- The quantity of each coating and surface preparation product.
The VOC content (pounds per gallon) of each coating and surface preparation product after mixing according to the manufacturer's instructions. Safety Data Sheets (SDS) for each product will also list VOC percentages.
OSHA Requirements for Paint Technician Safety
The OSHA requirements outlined below apply to most shops. However, this list does not include every applicable OSHA regulation. It is important to view the actual OSHA regulations to ensure you are in compliance.
Ventilation: What You Need To Know
OSHA Standards require that mixing room ventilation provide “…for a complete change of air within the room at least six times per hour.” This can be most easily achieved with mechanical ventilation. For more information, see the “Paint Mixing Room Guidelines and Best Practices” fact sheet.
Sanding Activities
If possible, use vacuum sanders or a ventilated prep table while sanding. If exposures exceed OSHA permissible exposure limits, workers will need to wear appropriate respirators. Only use NIOSH approved N95 masks – the mask will be clearly labeled. A half-mask air purifying respirator with an appropriate particulate filter will likely provide adequate protection for sanding activities (depending on actual workplace exposures) [29 CFR 1910.134(a) and (d)(3); 29 CFR 1910 Subpart Z].
Solvent Wipe-Down Tasks
If possible, perform wipe-down tasks in a booth or near adequate ventilation, because the ventilation will remove the solvent vapors from the air and benefit all workers. If exposures exceed OSHA permissible exposure limits, workers will need to wear appropriate respirators. A NIOSH approved N95 half-mask air purifying respirator with an organic vapor filter will likely provide adequate protection for solvent wipe-down tasks (depending on actual workplace exposures) [29 CFR 1910.134(a) and (d)(3); 29 CFR 1910 Subpart Z].
Spray Booths
OSHA has mandatory ventilation requirements for spray booths (e.g., 29 CFR 1910.94(c)(5)) but these are generally similar to the EPA requirements noted above. Shop owners must ensure that spray booths and prep stations have ventilation systems that are in good operating condition and filters are changed according to manufacturers’ recommendations.
Personal Protective Equipment (PPE): What You Need To Know
Protect Your Lungs
While painting, technicians must be properly protected with loose-fitting supplied-air-respirators (SARs) or better (assigned protection factor of at least 25). Note that a higher level of protection may be needed depending on actual exposure levels [29 CFR 1910.134(a)(2(d)(3); 29 CFR 1910 Subpart Z)]. SARs provide a much higher level of protection than air-purifying respirators that use cartridges. All respirator cartridges must be stored in airtight plastic bags when not in use, as the cartridges will continue to absorb particles and chemicals that are in the air – even when not worn – and have a limited lifetime.
Protect Your Skin
Nitrile or other impermeable protective gloves must be worn while sanding, performing solvent wipe downs, and working with paints and solvents [29 CFR 1910.138]. Ensure that workers also change their gloves frequently enough and avoid using torn, damaged, or leaky gloves to ensure continued skin protection. Workers must also be equipped with skin protection—examples include coveralls, a paint suit, and a headsock (unless a hooded respirator is used) [29 CFR 1910.132(a)].
Protect Your Eyes
Paint technicians must wear eye protection such as safety glasses, goggles or a hooded or full face-piece respirator when working with paints and solvents [29 CFR 1910.133(a)(1)].
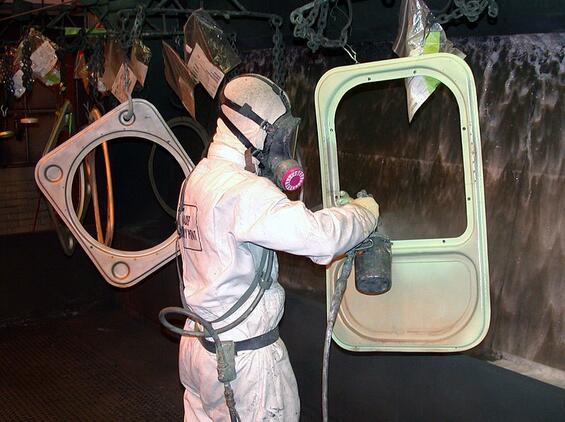
An example of a supplied air respirator.
Hazard Communication: What You Need To Know
Safety Program Requirements
You must develop and maintain the following safety programs in your auto body shop:
Written Respiratory Protection Program
Respiratory protection programs [29 CFR 1910.134(c)] ensure that the shop only uses NIOSH-approved N95 respirators meant for that specific task [29 CFR 1910.134(d)]. The California Department of Industrial relations has created guidance on creating a respiratory protection program. All respiratory programs require:
- Medical evaluations for all workers who must wear respirators.
- Annual fit tests for workers that wear tight-fitting face piece respirators.
- Confirmation that those wearing tight-fitting face piece respirators do not have facial hair that would interfere with the respirator seal.
- Appropriate filter change-out schedules for all air-purifying respirators worn in the shop.
Written Hazard Communication Program
A written hazard communication program [29 CFR 1910.1200(e)] ensures that:
- The shop has copies of safety data sheets (SDSs) for all hazardous chemicals which are easily accessible to workers at all times.
- Workers receive training on the hazards of the chemicals in their workplace. This includes informing workers about where hazardous chemicals are present, how to read product SDSs and labels, and the measures employees can take to protect themselves from hazards.
Find Additional Information
- The Massachusetts Office of Technical Assistance (OTA) Guidance for Compliant Spray Booth Operation fact sheet outlines state and local regulations. In addition, OTA staff can provide free and confidential assistance to your business. Email OTA at maota@mass.gov or call 617-626-1060 for assistance.
- The Massachusetts Department of Labor Standards offers a free OSHA consultation service to help you recognize and control health and safety hazards in your workplace. However, if you fail to eliminate or control identified "serious" or "imminent danger" hazards it may result in a referral from consultation to an OSHA enforcement office. Enforcement situations are very rare, and companies speak very highly of their experience working with staff.
- The California Department of Public Health has an Isocyanates: Working Safely fact sheet that outlines risks and safety plans for auto body shops to prevent worker exposure.
- OSHA has developed an auto shop website that covers industry specific health and safety requirements.
Contact
Phone
You will be connected to the person who can best answer your questions.