9.1 Introduction to the Pavement Design Process
Effective pavement design is one of the more important aspects of project design. The pavement is the portion of the roadway which is most obvious to the roadway user. The condition and adequacy of the roadway is often judged by the smoothness or roughness of the pavement. Deficient pavement conditions can result in increased user costs and travel delays, braking and fuel consumption, vehicle maintenance repairs and increased probability of crashes.
The pavement life is substantially affected by the number of heavy load repetitions applied, such as single, tandem, tridem and quad axle trucks, buses, tractor trailers and equipment. A properly designed pavement structure will take into account the applied loading.
To select the appropriate pavement type/treatment and properly design a pavement structure, the Designer must obtain information and input from the Pavement Management System (PMS), the Pavement Design Engineer (PDE), and Research & Materials. The Designer must also apply sound engineering judgment. Steps in the design process include:
- Review Pavement Management Data to determine the appropriate scope of work and treatment type (i.e., new pavement, reconstruction, reclamation, resurfacing, or pavement preservation).
- Evaluate existing pavement to confirm the scope of work and determine preliminary design and appropriate construction strategy. Research roadway history and traffic data, verify existing pavement materials and structure. Perform field trips to make site inspections, prepare a pavement condition checklist, communicate with engineering and maintenance forces for history of roadway performance, groundwater problems and other background information.
- Evaluate sub-base and sub-grade for drainage characteristics and bearing capacity.
- Make structural calculations. The traffic, soils, and existing pavement data is used to calculate specific pavement course requirements.
- Set specifications. The pavement materials, construction methods, and finished project requirements must be both practical to attain and clearly defined. The Designer must ensure that the plans, specifications, and estimate clearly and unambiguously define the requirements.
The pavement design procedures contained in this chapter are based on the 1972 AASHTO Interim Guide as revised in 1981. These are the standard procedures to be followed for the design of all pavement structures subject to this chapter.
For Hot Mix Asphalt (HMA) structural resurfacing on Interstate and other controlled access highways, the design procedures contained in the 1993 AASHTO Guide for Design of Pavement Structures may be utilized, subject to the review and approval of the PDE. The 1993 AASHTO Guide features the following:
- Use of statistical reliability instead of the factor of safety design
- Use of resilient modulus tests for soil support (a dynamic test) vs. CBR (a static test)
- Introduction of environmental factors to evaluate the effects of spring thaw and frost heave
New pavement design methods are being implemented on a limited basis across the United States. The “AASHTO Mechanistic-Empirical Pavement Design Guide” (M-E Design Guide) was released in 2004 with the goal of improving the existing pavement design procedures. The M-E Design Guide transitions from the existing empirical-based pavement design procedures to mechanistic-empirical based procedures. It employs analytical modeling capabilities and incorporates the pavement field performance data collected under the Strategic Highway Research Project (SHRP). MassDOT is currently engaged in Phase III of implementation of the AASHTO M-E Design Guide.
The standard pavement cross-section details to be applied to pedestrian and bicycle facilities are provided in Chapter 11 and other applicable chapters in the PDDG.
9.2 Pavement Types, Definitions, and Abbreviations
Different types of pavement are commonly used in the construction of roadways. There are three different types of pavement. These are:
- Flexible Pavement
- Rigid Pavement
- Composite Pavement
Each of these pavement types is presented below.
Flexible Pavement
This chapter outlines the design methods for flexible pavement (Hot Mix Asphalt (HMA) and also known as bituminous concrete). A flexible pavement structure consists of the following layers – the sub-base, base course, intermediate course, surface course, and where determined necessary, a friction course.
- The sub-base consists of granular material - gravel, crushed stone, reclaimed material or a combination of these materials.
- The base course is an HMA or concrete pavement layer placed upon the compacted sub-base. A gravel base course can be designed and specified for low volume roadways (<2,000 vehicles per day) depending upon loading and other design considerations.
- The intermediate course is an HMA pavement layer placed upon the base course.
- The surface course is the top HMA pavement layer and is placed upon the intermediate course.
- A friction course is a specialized thin-lift wearing course which, when specified, is placed over the surface course. Friction courses provide improved vehicle skid resistance, but do not provide any structural value to the pavement. Typically friction courses are placed on high volume limited access roadways.
Typical cross-sections illustrating the pavement courses for high and low traffic volume roadways are shown in Figure 9‑1. High volume roadways should have all of the courses listed above, and if necessary, a friction course, while low volume roadways do not require an HMA base course between the gravel sub-base and the HMA intermediate course.
Figure 9-1: Pavement Courses for Flexible Pavement Structure
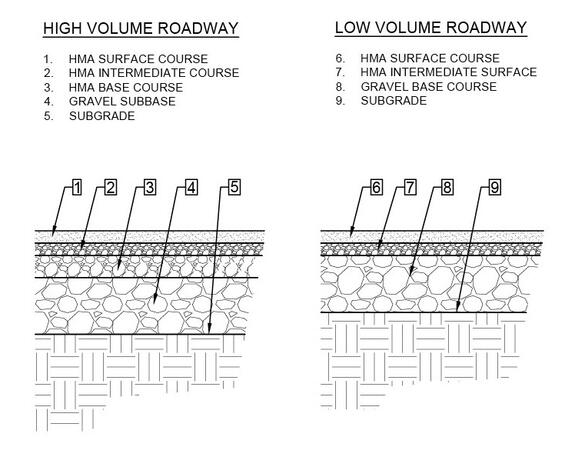
Source: MassDOT
Rigid Pavement
Because Massachusetts highways are primarily HMA, the design for rigid pavements is not detailed in this Guide. A rigid pavement is constructed of Portland cement concrete (PCC) placed on a granular sub-base. PCC pavements are either plain and jointed or continuously reinforced. All newly constructed or rehabilitated rigid pavements shall be designed as directed and approved by the PDE.
Composite Pavement
A composite pavement consists of one or more HMA pavement courses over a PCC base. All newly constructed or rehabilitated composite pavements shall be designed as directed and approved by the PDE.
Other Pavement Concepts
Research is continuing into porous and permeable pavements that have the potential to improve safety, reduce runoff and diminish undesirable environmental impacts. Some noise-reducing pavements are based on a similar premise. Permeable pavements may be constructed as full-depth porous pavements or surface friction courses.
Full-depth porous pavements are constructed using specialized asphalt layers or Portland cement concrete surfaces that permit water to drain down to a specially constructed crushed stone base. This crushed stone base functions as a temporary stormwater storage area and allows the runoff to infiltrate into the sub-grade. While this design concept appears promising for low volume facilities and parking areas, the foundation needed to adopt it on larger facilities is not in place at this time.
Permeable surface friction courses such as Open Graded Friction Course (OGFC) permit water to drain from the driving surface below the tire-pavement interface. This reduces hydroplaning, tire spray and tire noise while improving skid resistance and visibility. Several types of OGFC have been placed on Interstate and limited access highways in Massachusetts.
Experimental pavements have been constructed which feature the use of colored aggregate in the pavement surface to improve the visual consistency of the roadway with its surroundings. Other projects have been built which feature the use of colored aggregate to improve the definition between the roadway and shoulder or lanes intended for exclusive use by bicycles, buses or other specific types of roadway users. These practices may be considered in special circumstances.
Pavement Design Terms and Definitions
The following terms and abbreviations are commonly used in pavement design.
- Binder – The liquid asphalt material in an HMA mixture that bonds the aggregate together.
- Equivalent Single Axel Load (ESAL) – The conversion of mixed vehicular traffic into its equivalent single-axle, 18-Kip Load. The equivalence is based on the relative amount of pavement damage.
- Daily ESAL (T18) – The average number of equivalent 18-Kip loads which will be applied to the pavement structure in one day. Normally, a 20-year design period is used to determine the daily load. (See Table 9‑1).
- ESAL Applications per 1000 Trucks and Combinations – A factor which reflects the relative mix of sizes (see Table 9-1) and weights of trucks on various classes of highways (e.g., freeways, arterials, collectors, and local streets). Truck percentages typically exclude two-axle, four-tire pickup trucks, the effect of which may be ignored.
- Pavement Serviceability Index (PSI) – A measure of a pavement's ability to serve traffic on a scale of 0 to 5. It reflects the extent of pavement condition.
- Terminal Serviceability Index (Pt) – A pavement design factor which indicates the acceptable pavement serviceability index at the end of the selected design period (usually 20 years).
- Sub-grade – The undisturbed virgin substrate or embankment material which the pavement structure is placed upon.
- Bearing Ratio – The load required to produce a certain penetration using a standard piston in a soil, expressed as a percentage of the load required to force the piston the same depth in a selected crushed stone. Bearing Ration values are normally determined using the California Bearing Ratio (CBR) text method.
- Design Bearing Ratio (DBR) – The selected bearing ratio used to design the pavement. It is based on a statistical evaluation of the CBR test results on the soil samples.
- Soil Support Value (SSV) – An index of the relative ability of a soil or stone to support the applied traffic loads. It is specifically used for the pavement design method in the AASHTO Interim Guide for Design of Pavement Structures. The soil support value of the sub-grade is related to its CBR (DBR).
- Structural Number (SN) – A measure of the structural strength of the pavement section based on the type and thickness of each layer within the pavement structure.
- Layer Coefficient – The relative structural value of each pavement layer per inch of thickness. It is multiplied by the layer thickness to provide the contributing SN for each pavement layer.
- Skid Resistance – A measure of the coefficient of friction between an automobile tire and the roadway surface.
Table 9-1: Equivalent 18-Kip Axle Applications per 1,000 Trucks for Flexible Pavements
Highway Class | Equivalent Axle Applications |
---|---|
Freeways | 1100 |
Major Arterials | 880 |
Minor Arterials (Urban and Suburban) | 880 |
Minor Arterials (Rural) | 660 |
Collector (Urban and Suburban) | 880 |
Collector (Rural) | 660 |
Local Roads, Urban and Suburban | 660 |
Local Roads, Rural | 660 |
Source: MassDOT
9.3 Typical Pavement Design Procedures for Design Submittals
All pavement designs are determined by the designer with the MassDOT (PDE) responsible for reviewing and approving all pavement designs. The pavement design steps are summarized below and presented in detail in the following sections.
- Step 1: Determine which of the following five categories is the appropriate scope of work:
- New Pavement
- Reconstruction
- Reclamation
- Resurfacing
- Preservation Treatment
- Pavement for Pedestrian and Bicycle Facilities
- Step 2: Collect basic project data, including:
- Project identification
- Traffic data
- Existing pavement information
- Field inspection report
- Step 3: Determine Design Bearing Ratio (DBR)
- Step 4: Assemble and submit pavement design Information to PDE, during 25 Percent Design
- Pavement design checklist
- DBR and preliminary pavement design
- Project plans and profiles
- Traffic data
- Step 5: PDE reviews scope of work and DBR Determination
- PDE Reviews scope of work
- PDE approves DBR as submitted
- Use DBR from previous work
- Request subsurface exploration for new pavements
- Step 6: PDE Reviews/Comments on 25 Percent Design
- Step 7: PDE Reviews/Comments on 75 Percent Design
Step 1 - Determine Scope of Work
The Designer will determine the appropriate scope of work for the pavement design. This can be a new pavement, reconstruction, reclamation, resurfacing, pavement preservation, pedestrian/bicycle facility, or a combination of work. The scope of work may or may not include widening or corrective work to the existing pavement. To determine the scope of work for existing pavements (i.e., all work other than new pavement) the Designer shall review current Pavement Management data. Pavement Management reports will normally identify the apparent scope of pavement treatment required.
New Pavement
New pavement is a pavement structure placed on a prepared sub grade. It applies to new roadway construction, to a relocated roadway, or to the new part of a widened roadway.
Pavement Reconstruction
Reconstructed pavement or full depth reconstruction results when an existing pavement structure is completely removed to the sub-grade and replaced with a new pavement structure. This type of work is needed when the existing pavement has deteriorated to such a weakened condition that it cannot be salvaged with corrective action. The type and extent of pavement distress will determine when pavement reconstruction is necessary.
Pavement Reclamation
Reclaimed pavement reuses an existing pavement structure through the pulverizing and mixing of the existing pavement and granular sub-base into a gravel base material to be overlaid with new HMA layers. The reclamation method is usually performed on site.
Pavement Resurfacing
Pavement resurfacing consists of placing the needed thickness of hot mix asphalt on an existing pavement. The resurfacing will return the pavement to a high level of serviceability and provide the necessary structural strength for the pavement design period.
Pavement Preservation
Pavement preservation involves the application of properly timed surface treatments to ensure that pavements in good condition will remain in good condition. Preservation treatments extend the pavement service life, but generally provide no structural strength.
Pedestrian and Bicycle Facilities
Pavements for pedestrian and bicycle facilities shall be designed as presented in Chapter 11 and other applicable chapters of the PDDG. All project designs must meet ADA standards.
Step 2 - Collect Basic Project Data
The designer must collect the basic project data listed in the PDDG Checklist and Submission Distribution Workbook (PDDG 9-A-1, Pavement Checklist), along with a Field Inspection Report, as described below.
Project Identification
Provide the project location information and project design engineer.
Traffic Data
At a minimum, the following traffic data is required:
- Current ADT, (ADT for year of proposed opening to traffic)
- Projected ADT (20 years)
- ADT truck percentage
- Number of lanes
- Divided/undivided
- Source of traffic data
Existing Pavement Information
The thickness and type of each pavement layer (i.e., surface course, intermediate course, base course, sub-base ) and sub-grade information shall be recorded. This data is necessary for proper design and analysis of the pavement structure for all types of projects. Base plans and profiles should also be obtained for the purpose of pavement design.
Field Inspection Report
A field inspection report must also be prepared which includes the general condition of the roadway. The field report should note pavement deficiencies including type of distress, extent of distress and severity of distress (see Pavement Design Checklist). The report should also include other field observations such as:
- Adequacy of drainage
- Presence of curbing, edging, berm or shoulder condition
- Sidewalks
- Curb cuts and driveways
- Any other characteristic that may be pertinent to the analysis of the existing pavement and scope of work
The Designer should also research and document known problems with the existing pavement through discussion with field maintenance personnel.
Step 3 - Determine Design Bearing Ratio (DBR)
Table 9‑2 summarizes the recommended action to determine the Design Bearing Ratio based on the Daily ESAL (T18). Projects having T18 values less than 15 should use the minimum design for the roadway’s classification (refer to Table 9-5). Projects having T18 values between 15 and 120 should use DBR values based on AASHTO soils classification as shown in Table 9‑3. Projects having T18 values greater than 120 will require AASHTO soils classifications and CBR testing. Soil classification data and CBR test data should be submitted to the PDE for DBR determination.
Table 9-2: Design Bearing Ratio Determination
Value from Line (h) of Data Sheet 1 (T18) | Action |
---|---|
T18 < 15 |
Use Minimum Design (See Exhibit 9-11) |
15 < T18 < 120 | Assume DBR based on soil classification as determined by District lab (From Exhibit 9-5) |
T18 > 120 | Submit AASHTO soils classification and CBR test results to PDE for DBR determination and approval |
Source: MassDOT
Table 9-3: DBR Based on AASHTO Soils Classification
General Classification / Subgrade Rating | AASHTO Group Classification | DBR | SSVV |
---|---|---|---|
Granular Materials / Excellent to Good | A1 - a | 30 | 7.1 |
Granular Materials / Excellent to Good | A1 - b | 20 | 6.2 |
Granular Materials / Excellent to Good | A2 - 4 | 15 | 5.4 |
Granular Materials / Excellent to Good | A2 - 51 | ||
Granular Materials / Excellent to Good | A2 - 61 | ||
Granular Materials / Excellent to Good | A2 - 71 | ||
Granular Materials / Excellent to Good | A - 3 | 10 | 4.4 |
Silt-Clay Materials / Fair to Poor | A2 - 4 | 8 | 3.9 |
Silt-Clay Materials / Fair to Poor | A2 - 52 | 5 | 2.8 |
Silt-Clay Materials / Fair to Poor | A2 - 62 | 3 | 1.6 |
Silt-Clay Materials / Fair to Poor | A2 - 72 | 2 | 0.6 |
Virgin Gravel for Reconstruction | 40 | 7.8 | |
In-Site Gravel Base/Sub-base for Resurfacing | 8.5 | 6.6 |
Notes:
- Consult Pavement Design Engineer (PDE).
- Consider economics of replacing poor material
Source: MassDOT
Step 4 - Assemble and Submit Pavement Design Information to PDE during 25 Percent Design
The design engineer will perform a detailed analysis to determine the type and thickness of each course in the pavement structure. The design engineer will submit the recommended detailed pavement design with completed data sheets to the PDE. The types of analysis are discussed in the Section 9.4 Detailed Pavement Design Guidance by Scope of Work.
The designer should contact the PDE for guidance as needed.
The designer will submit all applicable information for the pavement design to the PDE including:
- The Pavement Design Checklist documenting the reasons for selecting the scope of work
- The DBR value and preliminary pavement design
- A set of project plans and profiles
- Traffic data
Step 5 - PDE Reviews Scope of Work and DBR Determination
The PDE will review the Designer's recommendation, scope of pavement work, the preliminary pavement design, traffic data and the pavement checklist documenting the engineered design solution. The PDE will provide comments on the scope of work and the preliminary pavement design.
Based on the scope of work and available test data, the PDE will determine the DBR in one of the following ways:
- PDE approves DBR as submitted – The PDE must approve the Design Bearing Ratio used for the design. The PDE will approve, reject, modify or request additional sampling and testing.
- Use DBR from previous work – If it is available and still applicable, the PDE will use the DBR used for the original pavement design or any previous pavement resurfacings.
- Request additional subsurface exploration – If the Designer recommends a subsurface exploration to determine the soil gradation, properties and stratification data and the PDE has concurred, the Designer will prepare and submit the plan to the MassDOT, Pavement Management Section. The subsurface exploration information will be shown on the project base plans and will include the required number and locations of test pits, pavement cores, etc.
Step 6 - PDE Reviews/Comments on the 25 Percent Design
The PDE will review and comment on the pavement design analysis and 25 Percent Design recommendation from the Design engineer.
Step 7 - PDE Reviews/Comments on the 75 Percent Design
The PDE will review and comment on the pavement design analysis and 75 Percent Design recommendation from the Design engineer.
9.4 Detailed Pavement Design Guidance by Scope of Work
New and Reconstructed Pavements
This section specifies the MassDOT procedure for determining the detailed design of a new or reconstructed pavement. This procedure applies to HMA pavements only.
MassDOT uses the AASHTO Interim Guide for Design of Pavement Structures as the basic design methodology. However, MassDOT has incorporated several modifications to the Guidebook’s procedures to reflect specific conditions in Massachusetts and to simplify the procedure.
The designer should complete the New or Reconstructed Pavement Form (cover sheet and data sheets 1 through 3) and submit it to the PDE prior to the 75 Percent Submittal. For reference, the designer can view Sample Problems and Completed Forms.
Pavement Design Cover Sheet
The following information must be recorded on the cover sheet:
- Enter the project identification data at the top of the cover sheet.
- Summarize the recommended pavement design by documenting the surface, base, and sub-base data. List the depths, type of layer, and recommended lifts.
- Describe the special borrow, if required for the project. Special borrow may be necessary where the existing sub-grade is susceptible to frost penetration within the typical frost penetration depth. If this subsurface condition exists, subsurface exploration and soil analysis may be warranted. The Designer will recommend the type and depth of special borrow to be used for frost control. Special Borrow is generally placed on freeways and arterial routes. Consideration for placement on other roads will depend on functional classification, traffic volumes, presence of utilities, construction methods, etc.
Data Sheet 1: Pavement Structural Design Data
Data Sheet 1 includes the following information:
- Line (a): Enter the anticipated (current) ADT for date of opening.
- Line (b): Enter the future ADT (see Chapter 3 for information on traffic volume forecasts). Generally the design period for pavements is 20 years; however there may be occasions when the traffic information submitted does not cover the design period. In these cases the future ADT is to be estimated by approved methods. Under certain circumstances, pavements may be designed for periods of less than 20 years.
- Line (c): Calculate the average ADT during the design period.
- Line (d): Calculate the average ADT in one direction.
- Line (e): Enter the truck percentage for the ADT.
- Line (f): Calculate the average daily truck volume in one direction.
- Line (g): Enter the equivalent 18-Kip axle application per 1,000 trucks and combinations (See table 9-1).
- Line (h): Calculate the number of 18-Kip axle loads per day in one direction (T18).
Design Bearing Ratio (DBR) Determination
Use the value on Line (h) (T18) and Table 9‑2 to determine the sub-grade or Sub-base DBR. As noted, the PDE may be required to provide the DBR. In all cases, Designers make a general computation of the sub-grade or sub-base DBR for reviews by the PDE, as described in the Section 9.3 Typical Pavement Design Procedures for Design Submittals.
Data Sheet 2: Determining Structural Number (SN)
The following steps are required to determine the structural number (SN):
- Step 1: Determine the design lane equivalent daily 18-Kip applications based on the number of lanes.
- Step 2: Determine the DBR for the sub-grade from Tables 9‑2 and 9‑3. The sub-base DBR is 40 for the typical MassDOT sub-base on new or reconstructed pavements (gravel).
- Step 3 Determine the soil support value (SSV). Figure 9‑2 illustrates the relationship between the DBR and SSV.
- Step 4: Determine the required structural number (SN) above the sub-base and above the sub-grade. Figure 9‑3 should be used. Use the design-lane T18 from Step 1 for the daily equivalent 18-Kip single axle load. Use the SSV from Step 3 for the soil support value.
- Step 5: Increase the SN by 15 percent to determine the design SN to adjust for climatic and other environmental conditions.
Figure 9-2: DBR Versus SSV
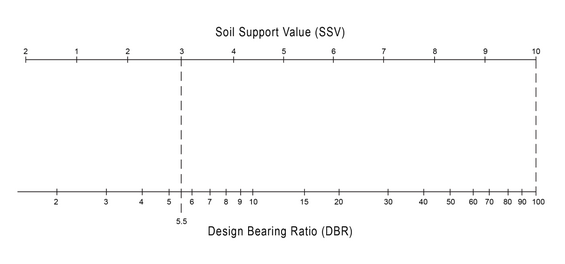
Source: MassDOT
Figure 9-3: Structural Number Nomograph (For Flexible Pavement P=2.5)
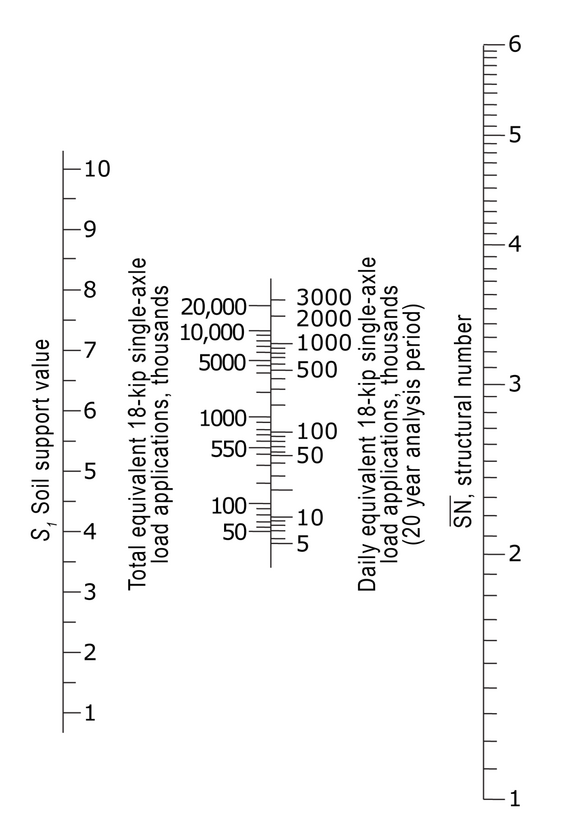
Note: The right side of the vertical line in the center provides the daily equivalent 18-kip single-axle load. It is only good for a 20-year analysis period. The left side provides the total load application, and it can be used for any design analysis period.
Source: Interim Guide for Pavement Structures. AASHTO. 1972
Data Sheet 3: Pavements Structural Number (SN)
By trial and error, the designer will select the most cost-effective design that provides the required SN for the highway conditions. The designer should also consider minimum and maximum lift thicknesses and the logistics of construction procedures when designing the pavement design combinations using this procedure.
- Step 1: Select each pavement layer component and the thickness of each layer.
- Step 2: From Tables 9-4 and 9‑5 select the layer coefficient for each pavement layer.
- Step 3: Determine the contributing SN for each pavement layer by multiplying the layer coefficient by its thickness.
- Step 4: The minimum thicknesses of each layer are noted on Table 9‑6.
- Step 5: Check to ensure that the required SN is provided above the sub-base and the sub-grade. If not, increase the layer thickness as necessary. If the trial design exceeds the required SN, reduce the layer thicknesses.
- Step 6: Determine several alternate pavement designs which satisfy the SN requirements. The selected design will be based on economics.
- Step 7: Regardless of the calculations from the pavement design analysis, the minimum design thickness should not be less than those shown in Table 9‑6.
Table 9-4: Pavement Layer Thicknesses
Pavement Course | Mix Type | Minimum Design Thickness | Maximum Design Thickness | Designation |
---|---|---|---|---|
Friction Course | Open Graded | 1 | 1.25 | OGFC-AR; OGFC-P** |
Surface Course | 9.5MM | 1.25 | 1.75 | SSC-9.5;SSC-9.5 P |
Surface Course | 12.5MM* | 1.75 | 2.5 | SSC-12.5;SSC-12.5 P |
Surface Course | 12.5MM | 1.25 | 2.5 | ARGG-12.5 |
Intermediate Course | 12.5MM | 1.75 | 2.5 | SIC-12.5 |
Intermediate Course | 19.0MM | 2.25 | 3.5 | SIC-19.0 |
Base Course | 37.5MM | 3.50 | 5 | SBC-37.5 |
Leveling Course | 9.5MM` | 1 | 1.75 | SLC-9.5 |
Leveling Course | 12.5MM | 1.5 | 2.75 | SLC-12.5 |
Source: MassDOT
Notes:
*AR designation is for Asphalt Rubber Modified Binder
**“P” Designation is for Polymer Modified Asphalt Binder
***SSC-12.5 P is the preferred mixture
Table 9-5: Layer Coefficients for New and Reconstructed Pavements
Pavement Course | Placement Component | Layer Coefficient (per Inch) |
---|---|---|
Surface Course | HMA Riding Surface and Binder | 0.44 |
Base Course | HMA | 0.34 |
Sub-Course | Crushed Stone (Dense Graded) | 0.14 |
Sub-Course | Gravel | 0.11 |
Source: MassDOT
Table 9-6: Minimum Pavement Thickness (New and Reconstructed Flexible Pavements)
Pavement Course | Highway Type | Thickness (Inches) | Layer Coefficient | Structural Number (SN) |
---|---|---|---|---|
HMA Surface Course | Freeway | 1.75 | 0.44 | 0.77 |
HMA Surface Course | Arterial | 1.75 | 0.44 | 0.77 |
HMA Surface Course | Collector & Local | 1.50 | 0.44 | 0.66 |
HMA Surface Course | Low Volume | 1.50 | 0.44 | 0.66 |
HMA Intermediate Course | Freeway | 2.00 | 0.44 | 0.66 |
HMA Intermediate Course | Arterial | 1.75 | 0.44 | 0.88 |
HMA Intermediate Course | Collector & Local | 1.75 | 0.44 | 0.77 |
HMA Intermediate Course | Low Volume | 2.50 | 0.34 | 0.85 |
HMA Base | Freeway | 4.50 | 0.34 | 1.53 |
HMA Base | Arterial | 3.50 | 0.34 | 1.19 |
HMA Base | Collector & Local | 3.50 | 0.34 | 1.19 |
HMA Base | Low Volume | 12" gravel base | 0.11 | 1.32 |
Sub-base: Stone | Freeway | 4" stone | Stone - 0.14 | Stone - 0.56 |
Sub-base: Gravel | Freeway | 8" gravel | Gravel - 0.11 | Gravel - 0.88 |
Sub-base: Stone | Arterial | 4" stone | Stone - 0.14 | Stone - 0.56 |
Sub-base: Gravel | Arterial | 8" gravel | Gravel - 0.11 | Gravel - 0.88 |
Sub-base: Stone & Gravel | Collector & Local | 12" gravel | 0.11 | 1.32 |
Total Structural Number | Freeway | N/A | N/A | 4.62 |
Total Structural Number | Arterial | N/A | N/A | 4.17 |
Total Structural Number | Collector & Local | N/A | N/A | 3.94 |
Total Structural Number | Low Volume | N/A | N/A | 2.83 |
Source: MassDOT
Table 9‑6 is only valid when the conventional design calculations indicate a required pavement structure less than above. All pavement thicknesses shall be designed as detailed here. The use of crushed stone as part of the base course serves two purposes: it makes a firmer base for the paving machines, and it reduces the amount of gravel required. Gravel also serves two purposes: structural support (although it is weaker than crushed stone) and drainage. Crushed stone is incompatible with drainage and, therefore, cannot fully replace gravel.
Reclamation
For reclaimed pavements, the Designer will determine the depth of reclamation required. A minimum 12- inch granular base or sub-base course must be provided beneath the HMA pavement courses. The Designer must complete the Pavement Design Form as described in Section 9.4 Detailed Pavement Design Guidance by Scope of Work: New and Reconstructed Pavements.
The designer will take and analyze test pits to the depth to be recycled and provide the following information in the construction documents for each:
- The location of the test pit
- The depth of existing asphalt pavement material to be recycled
- The aggregate gradation of the underlying material to be recycled
Any gradation deficiencies in the existing materials, as indicated by the test pits, shall be corrected by blending the appropriate aggregate size(s) into the mixture.
Designers should be familiar with the construction procedure detailed in Subsection 403 of the Standard Specifications for Highways and Bridges.
Pavement Resurfacing
A pavement resurfacing can be used if the Designer determines that an existing pavement is in reasonably good condition. A pavement resurfacing may be in conjunction with roadway widening and/or corrective work to the existing pavement. The designer should complete the Pavement Resurfacing Design Form. For reference, the designer can view Sample Problems and Completed Forms. The depth of HMA resurfacing will be determined by the following procedure.
Pavement Resurfacing Design Cover Sheet
The following information must be recorded on the Pavement Resurfacing Design Coversheet:
- Enter the project identification data at the top of the cover sheet.
- Document the existing pavement structure before resurfacing.
- Record the recommended pavement resurfacing thickness.
Data Sheet 1: Pavement Structural Design Data
Data Sheet 1 should be completed using the following procedure:
- Line (a): Enter the current ADT.
- Line (b): Enter the future ADT, (see Chapter 3 for information on traffic forecasts) usually for 20 years beyond the current. Note that the traffic data available may not correspond to the dates in Lines (a) and (b). If not, the designer should assume a uniform straight-line increase between the data. This assumption can then be used to determine the traffic volumes in Lines (a) and (b).
- Line (c): Calculate the average ADT during the design period.
- Line (d): Calculate the average ADT in one direction.
- Line (e): Enter the truck percentage for the ADT.
- Line (f): Calculate the average daily truck volume in one direction.
- Line (g): Enter the equivalent 18-Kip axle application per 1,000 trucks and combinations (See Table 9-1).
- Line (h): Calculate the number of 18-Kip axle loads per day in one direction (T18).
- Line (i): Calculate the design lane equivalent daily 18-Kip applications based on number of lanes.
- Line (j): Enter the sub-grade DBR and SSV. These will be provided by the PDE as discussed in "Step 3 – Determine DBR” and Tables 9-2 and 9-3.
- Line (k): Determine the required SN above the sub-grade from Figure 9-5.
- Line (l): Determine the design SN by increasing the SN by 15 percent.
Data Sheet 2: Actual SN of Existing Pavement
The following steps are required to complete Data Sheet 2:
- Line (a): Enter the SSV of the existing pavement elements. The SSV for the penetrated crushed stone base, the sand bound crushed stone base, and the gravel sub-base are usually assumed as shown. However, if laboratory-determined DBR results are available, these values should be used. Enter the SSV for the sub-grade from Line (j) of Data Sheet 1.
- Line (b): Determine the SN of the existing pavement. Follow these steps:
- Table 9‑5 provides the layer coefficient for each layer component for a new pavement.
- The coefficients in Table 9‑7 should be multiplied by a reduction factor (RF) from Table 9‑8. The RF will be based on a visual survey of the type and extent of distress in the existing pavement. The RF will apply even if corrective work is performed on the existing pavement.
- The contributing SN for each layer is calculated by multiplying its depth by the layer coefficient and RF.
- The total SN is found by summing the SN of each pavement layer.
(Note: If Portland Cement Concrete is part of the existing pavement, the PDE will determine its contributing SN.)
- Line (c): Determine the actual SN above each layer of the existing pavement. The SN for each layer is entered in the appropriate column. The "Total SN" reflects the cumulative SN above each pavement layer.
Table 9-7: Layer Coefficients for Existing Pavements
Pavement Course | Placement Component | Layer Coefficient (per inch) |
---|---|---|
Surface Course | HMA | 0.44 |
Surface Course | Sand Asphalt | 0.40 |
Base Course | HMA | 0.34 |
Base Course | Asphalt Treated Penetrated Stone / Macadam | 0.24 |
Base Course | Crushed Stone / Macadam | 0.24 |
Base Course | Sand Bound Crushed Stone | 0.14 |
Base Course | Sandy Gravel | 0.07 |
Sub-base | Crushed Stone (Dense Graded) | 0.14 |
Sub-base | Gravel | 0.11 |
Sub-base | Sand / Sandy Clay | 0.05 to 0.10 |
Note: These are the layer coefficient values for when the pavement was new. They must be reduced according to the Reduction Factors in Table 9-8.
Source: MassDOT
Table 9‑8: Reduction Factors for Existing Pavement
Description of Existing Pavement | Reduction Factor (RF) |
---|---|
HMA surface exhibits appreciable cracking and crack patterns, little or no spalling along the cracks, some wheel path deformation, and is essentially stable. | 0.5 - 0.7 |
HMA surface exhibits some fine cracking, small intermittent cracking patterns, and slight deformation in the wheel paths, and obviously stable. | 0.7 - 0.9 |
HMA surface generally uncracked, little or no deformation in the wheel paths, and stable. | 0.9 - 1.0 |
Note: Description is based on a visual survey of the type and extent of distress. If the pavement distress and deterioration is worse than described in the table, consider removal and reconstruction of the pavement.
Source: MassDOT
Data Sheet 3: Determination of Resurfacing Thickness
The following steps are needed to complete Data Sheet 3:
- Line (a): Determine the required SN above each layer of the existing pavement using Figure 9‑3. The values from Line (i) on Data Sheet 1 and from Line (a) of Data Sheet 2 are used in the figure. The SN values from Figure 9‑3 are increased by 15 percent to determine the design SN.
- Line (b): Determine the SN deficiency for each layer for the existing pavement. The required SN from Line (a) of Data Sheet 3 is entered in the first column. Enter the value from Line (c) of Data Sheet 2 in the second column. The first column SN minus the second column SN yields the SN difference, which is entered in the third column. (Note: A negative value indicates there is no SN deficiency for that pavement layer.
- Line (c): The largest SN deficiency from the table in Line (b) is used to determine the thickness of the pavement resurfacing. The SN per inch is 0.44 for the Hot Mix Asphalt surface course. Regardless of the calculation, the minimum overlay thickness is 1 ¾ inch for modified top course.
Limited Access Highway Pavement Resurfacing Design
Due to the high traffic volumes and loadings on limited access highways, MassDOT maintains the ability to perform non-destructive testing and evaluate the pavement and subsurface conditions for these roadways. When designing structural resurfacings on limited access highways, the PDE may elect to use non-destructive testing to determine the appropriate resurfacing. The following general parameters are considered the minimum standards for these roadways:
Design Method
Both a layered component analysis and non-destructive testing analysis should be reviewed to calculate the effective existing SN.
Serviceability
An initial serviceability no greater than 4.5 should be assumed. A terminal serviceability no greater than 2.75 should be selected.
Reliability
Traffic disruption and congestion associated with construction operations result in significant user costs. Increased design reliability helps reduce these user costs. Thus, reliability levels approaching 99.9 percent are used to design structural resurfacings on the Interstate Highway System. Reliability levels approaching 99.5 percent should be used to design structural resurfacings on other limited access highway.
Back-calculation
Non-destructive testing must be analyzed to determine the resilient modulus of the soil. Because differing stress states occur between field conditions and lab conditions, a correction factor must be used to convert field-determined modulus values to lab values for design calculations. For granular soils, a resilient modulus correction factor (C) of 0.33 shall be used.
Depending upon the project, the back-calculated resilient modulus values of the sub-grade could vary significantly. Extremely high modulus values could be indicative of subsurface irregularities such as shallow bedrock or groundwater. To minimize the possibility of such erroneous modulus values, only modulus values within one standard deviation of the mean should be used to calculate the average resilient modulus for design purposes.
1993 AASHTO Pavement Resurfacing Design
Once the non-destructive testing has been analyzed and the future traffic loadings have been determined, the PDE will determine the required future structural number.
Typical Pavement Design for Low Volume Roads
In this revision of the PDDG, the minimum pavement cross section has been reduced for low volume roads (2,000 AADT maximum). This new minimum cross section has eliminated the use of HMA base course and provides for the placement of Gravel Base Course in its place. These revisions are reflected in Table 9-5 Minimum Pavement Thickness (New and Reconstructed Flexible Pavements).
To design pavements on low volume roadways, the Designer should begin with the minimum low volume roadway cross section as shown in Table 9-6. This design should be adequate for virtually all roadways less than 1,000 AADT and most roadways less than 2,000 AADT and 3 percent truck traffic. If the design calculations indicate that a greater thickness is required, then the Designer should adjust the pavement layer thickness accordingly.
Pavement Preservation
The design/selection of all pavement preservation treatments must be in coordination with the Districts and Pavement Management Office. The Designer shall submit the proposed treatment type and surface preparation requirements to the PDE for approval.
9.5 For Further Information
- Interim Guide for Design of Pavement Structures, AASHTO, 1972 (Revised 1993).
- Layered Pavement Design Method for Massachusetts, Massachusetts Department of Public Works and Massachusetts Institute of Technology, January, 1965.